结合生产实际。分析了影响磨料用酚醛树脂粘结剂粘度的几个因素。结果表明,苯酚与甲醛摩尔比为1:1.15~1:1.16,氨水占苯酚的4.6%一4.9%,用40 min左右的时间使物料升温至沸腾,后处理温度不高于75时,反应过程平稳,反应周期适中,所得到的酚醛树脂粘结剂的粘度较为适宜。
关键词:酚醛树脂;粘度;粘合剂
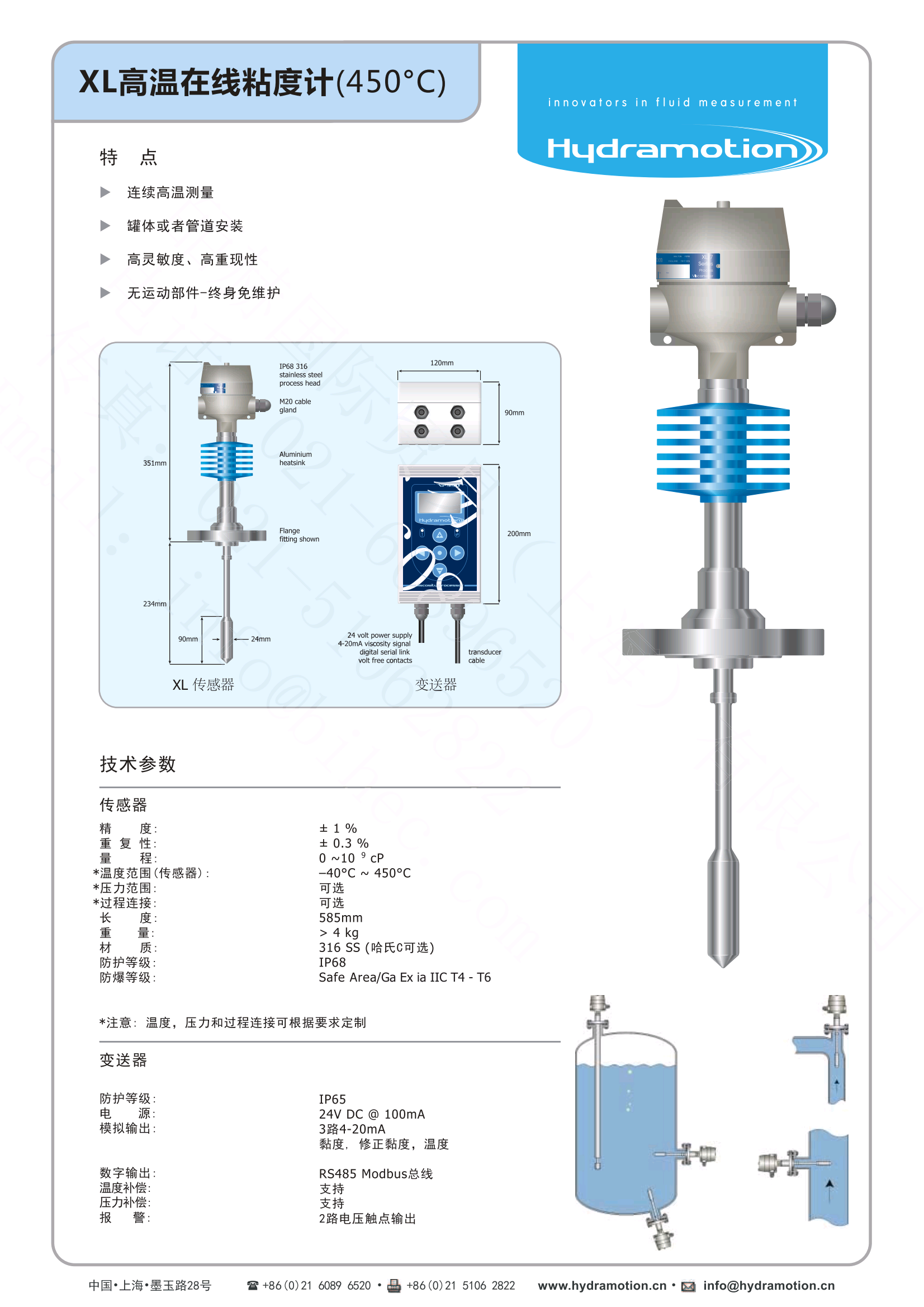
前言
酚醛树脂具有良好的机械性能,耐热性和加工成型性能,而且来源广,成本低,广泛用作砂轮的粘结
剂。酚醛树脂液的粘度直接影响对磨料表面的浸润均匀性。如果酚醛树脂液粘度太低,物料流动性大,成型
性差.容易粘模,制成的砂轮机械强度差;如果粘度过大,对磨料表面浸润性差,物料流动性差,混合不均
匀,不利于成型,制成的砂轮均匀性和机械强度也差。本文总结实际生产的经验,分析了控制酚醛树脂
结合剂的粘度的工艺方法,给出了适宜的工艺参数。
2试验
以氨水作催化剂,在PH>7的条件下,加热使苯酚和甲醛进行缩合反应生成甲阶段的酚醛树脂液。一
般应用厂家对树脂液的技术要求如表1所示。但是在实际应用中发现,树脂液的粘度在90~120 s时应用
效果最好。
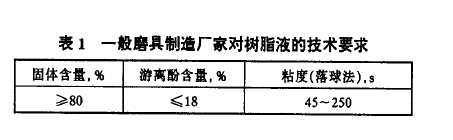
表2是通过实际生产中的数据,对苯酚甲醛比例、氨水比例、升温速度、后处理最高温度等因素对酚
醛树脂液粘度影响的分析。
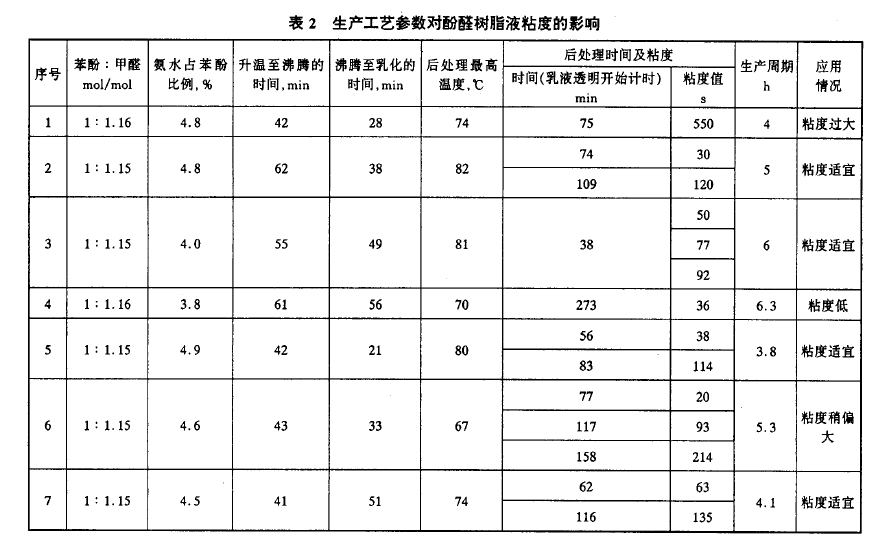
3、苯酚与甲醛比例对粘度的影响
随着甲醛含量的增加,反应速度加快,粘度增长快。1号与2号相比较,1号的沸腾至乳化的时间相
对2号缩短了26%;物料透明后大约75min后测粘度,1号已经达到了550 s,而2号仅为30 s。苯酚与
甲醛摩尔比在1:1.15~1.16为宜。
3.2氨水的用量对粘度的影响
比较1号与4号、2号与3号可以看出。氨水比例大时粘度增长速度都快,所得树脂的粘度也大。在苯
酚甲醛的摩尔比确定的情况下,可以通过增减氨水的用量来调整粘度的大小及反应速度的快慢。一般适宜
的氨水用量在4.6~4.9之间。
3.3升温速度对粘度的影响
反应初期的升温速度对反应速度和树脂粘度有一定的影响。比较2号与5号,升温速度慢反应平稳,
升温速度快粘度增长快。这与升温速度慢产生线性分子结构的树脂含量较大,升温速度快产生枝状分子结
构的树脂含量较大有关。升温速度过慢生产工时增加,所以可以适当提高反应初期的升温速度。一般控
制在40 min左右使物料沸腾为宜。
3.4后处理温度对粘度的影响
在后处理阶段,回升温度对粘度的影响也很大。温度越高,粘度增长越快,要严格控制回升温度,防止
凝胶化。比较6号与7号,在物料透明后118 min后。后处理的温度低的6号的粘度为93 s,而后处理的温
度高的7号的粘度为135 s。一般后处理的回升温度不能高于75为宜。
另外粘度中控合格后,需要将物料冷却到一定温度下放料,温度过低时,粘度增大,流动性差,放料时
间增加,温度过高,物料放出后在包装桶内继续反应,树脂粘度继续增大,甚至有凝胶化的可能。放料的温
度不能高于40。
4结论
综上分析,在产生砂轮粘结剂用酚醛树脂时,适宜的工艺参数如下:苯酚与甲醛的配比在1:1.15~
1.16,氨水用量在4.6~4.9之间;物料沸腾时间控制在40 min左右,后处理的回升温度不能高于75。
存贮的温度不能超过25,贮存时间不能超过1个月。
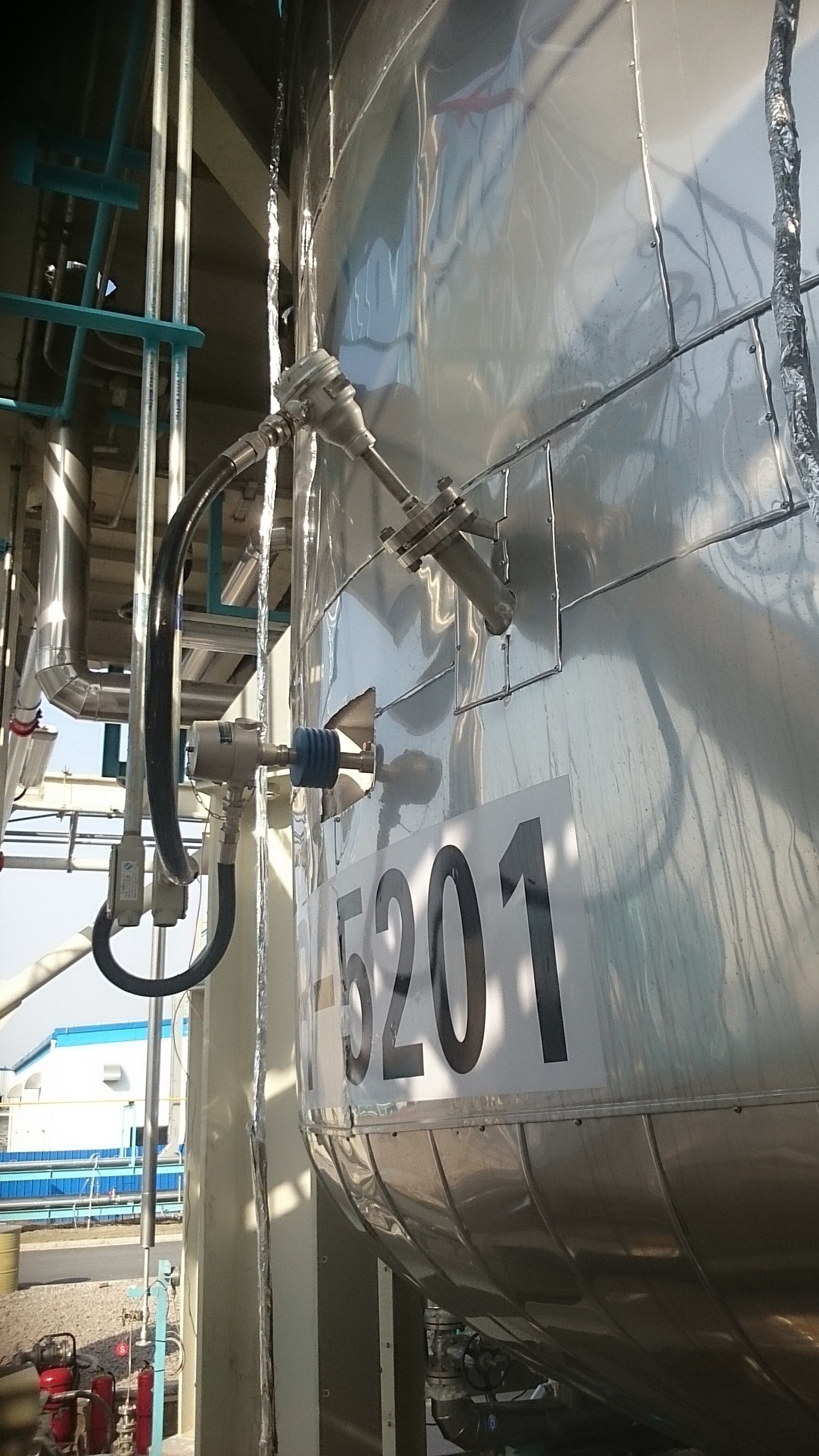